Session Aims & Scope
The aim of this session is to explore how digital twin technology, combined with artificial intelligence and safety technologies, is revolutionizing various industries. Its scope encompasses the latest advancements and applications of these technologies in sectors such as manufacturing, construction, robotics, and aerospace. Participants will gain insights into how digital twins can enhance efficiency, safety, and sustainability while also discussing the challenges and opportunities for future development. This session seeks to foster cross-disciplinary collaboration and innovation to drive the transformation of industries through digital twin technology.
Session Chair(s)
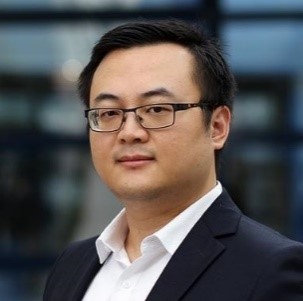
Chair
Li Yi
Associate Professor (Dr.-Ing.) ,Beihang University
liyibuaa@buaa.edu.cn
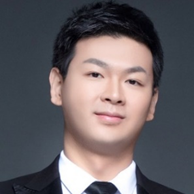
Co-Chair
Yupeng Wei
Associate Professor (PhD), Beihang University
yupengwei@buaa.edu.cn
Session Presentation
1.
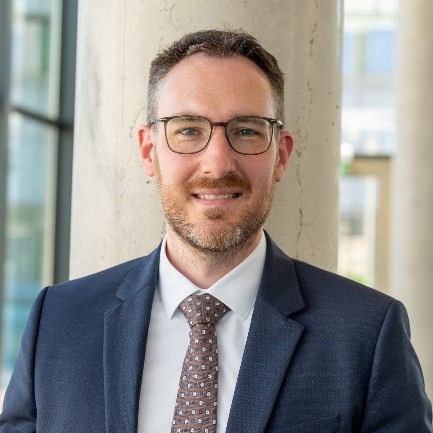
Benjamin Schleich
Professor (Dr.-Ing.),
Technical University of Darmstadt
Title: Digital Twins as Key Technology in Sustainable Manufacturing, Robotics and Space Applications
Abstract
The digital twin as a virtual representation of physical assets offers immense potentials for new business models and product-service-systems. Considering these benefits, the presentation will dive into the technological fundamentals of digital twins and will highlight state-of-the-art applications of digital twins in sustainable manufacturing, robotics, and space technology. Specifically, it will be shown how sustainability data models support the design of digital twins for CO2-efficient manufacturing and how digital process twins may support the realization of in-orbit small satellite factories. Beside this, future research directions are carved out.
2.
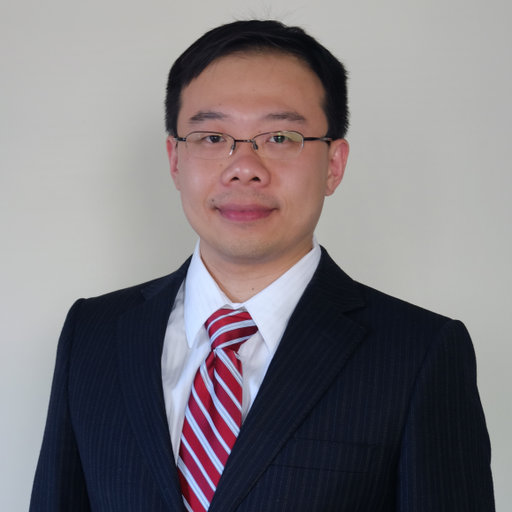
Dazhong Wu
Associate Professor (PhD),
University of Central Florida
Title: Industrial AI-enabled Smart Manufacturing: Methods and Applications
Abstract
Despite the broad range of applications for artificial intelligence (AI) in tasks such as image recognition and natural language processing, there are still challenges to implementing AI in the manufacturing industry. One of the main obstacles is the difficulty in integrating prior knowledge into machine learning to provide explanations for the decisions made by AI systems, as well as the challenge of ensuring that AI models can be generalized to different manufacturing settings. This presentation will explore the use of deep learning, physics-informed machine learning, and transfer learning in the context of manufacturing and the mechanics of additively manufactured materials. Specifically, it will showcase a deep learning model that predicts the temperature of the melt pool during a directed energy deposition process, a physics-informed machine learning model that incorporates the physics of the chemical mechanical planarization process, and a novel transfer learning framework that can predict the complex mechanical behavior of additively manufactured composites and lattice structures.
3.
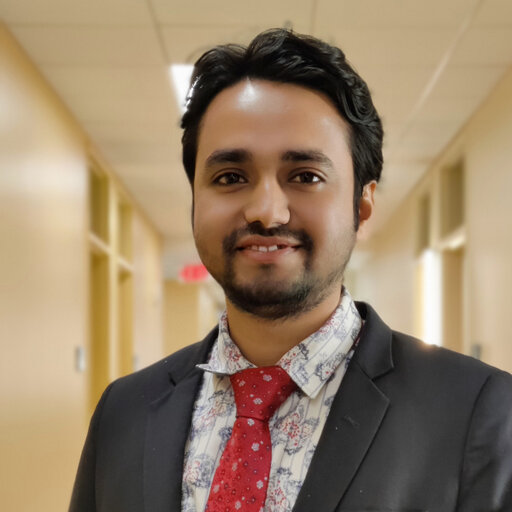
Md Hadisur Rahman
Graduate Research Assistant (M.S.),
West Virginia University
Title: Enhancing Worker Health and Safety in Construction Through Motion Capture Systems: Insights from Industry 5.0
Industry 5.0 emphasizes the collaboration between humans and intelligent systems, driving technological advancements across various sectors. In this context, Motion Capture (MoCap) technology plays a crucial role in enhancing worker health and safety in the construction industry by seamlessly integrating with these intelligent systems. The study analyzed 52 studies from the Scopus database, demonstrating the effectiveness of MoCap technology in reducing work-related musculoskeletal disorders and occupational hazards. The research revealed that marker less systems and wearable IMU sensors are widely used in construction. Finally, the study contributes to the body of knowledge on how MoCap technology ensures construction safety and offers suggestions for future research directions in line with Industry 5.0 principles.
4.
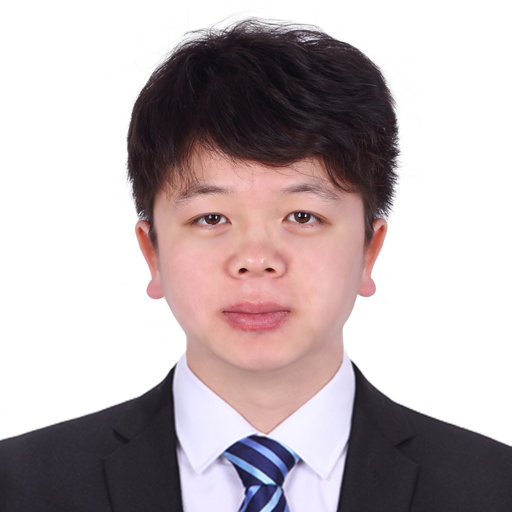
Shufei Li
Postdoctoral Research Fellow (PhD),
Nanyang Technological University
Title: Leveraging Large Language Models for Humanoid Cognition in Proactive Human-Robot Collaboration
Proactive Human-Robot Collaboration (HRC) aims for mutual-cognitive, predictable, and self-organizing teamwork between humans and robots, vital for human-centric smart manufacturing. To enable Proactive HRC, methods such as deep neural networks for visual detection, scene graphs for decision-making, and reinforcement learning for robot execution have been explored. However, these methods often need re-training with domain-specific datasets, limiting their generalizability. Large Language Model (LLM) technology offers a solution for understanding tasks, modeling human intentions, and planning robot actions using vision-language instructions. This paper explores humanoid cognition in Proactive HRC, evaluating LLM methods for task explainability, human-centricity, and robot executability, and discusses future integration prospects in manufacturing.
5.
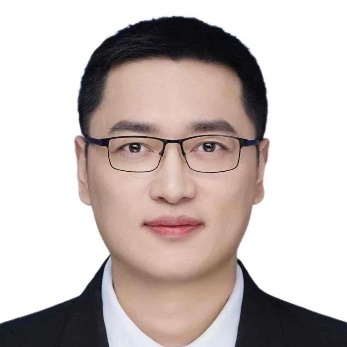
Lu-kai Song
Postdoctoral Research Fellow (PhD),
The Hong Kong Polytechnic University
Title: AI-driven system reliability framework and its application in aeroengine turbine blades
For complex engineering systems characterized by multi-level subsystems and multi-class modules, leading to the traditional integral or separate reliability framework are prone to unacceptable efficiency or accuracy. In response to this problem, by fusing the advantages of AI computing tools into large-scale system theory, an AI-driven system reliability evaluation framework is presented. In this framework, the complex problem is decomposed into several distributed sub-problems (i.e., multi-variate, multi-disciplinary and multi-objective), and establishes the mutually nested AI-based sub-models for multivariate response mapping, multi-disciplinary static/dynamic collaboration and multi-objective reliability evaluation. A typical system reliability evaluation problem (i.e., aeroengine turbine blades) is taken to validate the presented theoretical framework.